Challenging the Injection Molding Industry with DLS™ 3D Printing — ZVerse 3D Solutions
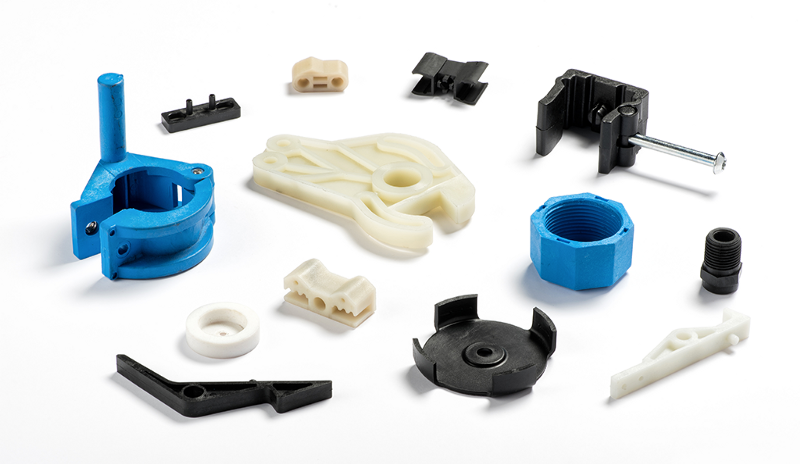
A common debate within manufacturing has been whether 3D printing could overcome enough obstacles to replace injection molding. But in past years, the gap between the two processes was too great to overcome for many reasons. And at the end of the day, injection molding offered the benefits of:
-Faster production speeds.
-Better mechanical properties.
-Superior finish quality.
-Lower cost on volume.
As a result, the two have remained largely complementary technologies. While injection molding offered better cost and speed for mass produced parts, 3D became a go-to option for rapid prototyping to significantly reduce development cost and time to market. 3D printing remained largely a development technology in environments that utilized injection molding.
Several reasons have held back 3D printing from making significant inroads against injection molding. One consideration was tolerance. While 3D printers could make parts very close to those produced with injection molding, tolerance issues remained. A second reason was quality. Depending on the end use of the injection molded part, 3D printed parts suffered from issues such as delamination and the lack of strong isotropic properties that were not at issue for injection molded parts. Third, layering and other visible effects caused by the deposition of materials during printing resulted in less than desirable finish quality that had to be improved through manual intervention such as sanding to achieve the desired surface finish. And finally, material selection within injection molding ranged into the hundreds of material types whereas options for 3D printed materials were initially limited to a smaller class of materials that comprised at most, a few dozen.
A New Process for Printing Parts
Today, revolutionary new printing processes are addressing those issues. Carbon3D’s proprietary Digital Light Synthesis™ process (DLS™) has quickly closed the gap to offer a process that can be ran on scale in production environments in direct competition with injection molding.
DLS™ technology uses Digital Light Synthesis™ — also known as digital light projection — and programmable resins to produce parts with superior and consistent mechanical properties that meet or exceed engineering grade quality. The printer projects UV light with a cross section of the part design through a window in the bottom of the resin tank. An oxygen-permeable membrane separates the window from the liquid and prevents the finished resin from attaching to the window itself. Carbon’s process is continuous and therefore offers higher speed than other processes. Estimates are that speeds can be up to 100 times faster compared to other printing methods.
As the process is continuous, it also produces parts with superior mechanical properties. Carbon’s process creates parts that are truly isotropic, eliminating issues such as delamination and other directional strength-related factors found in traditional printing. The consistency of the produced part and the elimination of layer lines not only strengthens the part, it creates superior surface finishes, again directly comparable to injection molded parts.
DLS™’s innovative approach solves the issues of tolerance, lack of isotropic strength and surface finishing to create engineering grade finished parts. And it does so at a speed acceptable for production environments. But the obstacles overcome by the printer also work in conjunction with an equally formidable partner — programmable resins.
Materials that Match the Process
Carbon’s DLS™ technology works in conjunction with its programmable resins. For most of the era since the advent of 3D printing, materials were often interchangeable from printer to printer. And while using photopolymerization is common in many types of 3D printing, Carbon takes the process further by adding chemistry to many of its resins that add strength and mechanical properties when used in the DLS™ process or through an additional heat application after printing that fast cures the part to bring it to final strength.
Materials offered by Carbon for the DLS™ process include:
Rigid Polyurethane — Consumer electronics, automotive, industrial material with excellent mechanical properties
Flexible Polyurethane — Used for fatigue resistant and flexible parts.
Elastomeric Polyurethane — Strong elastic performance with high tensile strength great for use in gaskets, seals and cushioning is required.
Cyanate Ester — Exhibits high temperature resistance and strength making it an excellent under the hood application for automotive.
Epoxy — High strength and abrasion for automotive, industrial and consumer applications.
Urethane Methacrylate — Strong and rigid parts are ideal for tooling and fixtures.
Dental Production 10 — Used heavily in dental applications for dies and models. The material can be reclaimed after use.
30 Silicone — High biocompatibility means parts produced can be worn comfortably on the skin. Excellent for use in consumer goods.
MPU 100 Material — Medical grade material that is durable, biocompatible and sterilizable.
Closing in — Benefits of Carbon 3D Printing Over Injection Molding
With its DLS™ technology, Carbon3D has created a symbiotic system of equipment and materials that addresses the issues that have long created a gap between 3D printing and injection molding. The resulting system offers several benefits for manufacturers and designers who have only been able to rely on injection molding in the past:
Design Freedom –
The additional strength provided by DLS™ and Carbon’s material offerings allow for greater design freedom by industrial and product designers. By taking advantage of complex geometries, designers can offer single parts that with injection molding may have had to be produced in pieces and joined. Textures can also be added at the initial production stage. With injection molding, texturing is often done at the final stage.
Unique or Unmoldable Parts –
With injection molding, due to the position of inner structures and cavities, parts may have been designed a certain way to accommodate certain physical limitations within the mold even though a better design was possible. With Carbon3D the strength and complexity of the process and materials allow better design iterations for specialty designs for industries such as automotive, aerospace and medical.
While 3D printing in general may never overtake injection molding as a primary production method, Carbon3D’s DLS™ system and line of materials has made the leap where others could not. For industries such as medical, automotive, aerospace and others requiring an agile, custom or unique production capability, Carbon3D’s DLS™ system can provide not only parts on par with injection molding, but in many cases, superior parts as well.
ZVerse’s unique platform allows any level of user to take advantage of DLS 3D technology. For beginners who have only drawings or sketches to those with just an idea and description, ZVerse can turn concepts into fully DLS optimized 3D files, which can in-turn be used to create end-use, production-quality mechanical components. Give ZVerse’s 3D Design solutions a try here.
Originally published at https://www.zverse.com on April 10, 2019.